论文部分内容阅读
摘要: 由于PLC外部的输入输出元件的可靠性不够好,而这些元件出现故障时PLC不会自动停机,从而造成不良后果。为了提高维修工作效率,及时发现元件故障,在没有酿成设备事故之前使PLC先停机、报警,有必要在PLC控制系统设计中采取故障检测措施。本文主要介绍了PLC常用的故障信号检测方法和故障信号显示方法,并举例说明了其程序设计方法。
关键词: PLC 故障检测 故障显示
可编程控制器本身具有很高的可靠性,在CPU操作系统的监控程序中有完整的自诊断程序,万一出现故障,借助自诊断功能可以很快找到故障部位,确定故障所在。但PLC外部的输入输出元件就不那么可靠,如行程开关、电磁阀、接触器等的故障率就很突出,而当这些元件出现故障时PLC不会自动停机,直到故障造成后果,如机械顶死、控制系统常规保护动作之后才会有所反应。为了提高维修工作效率,特别是为了及时发现元件故障,在还没有酿成设备事故之前使PLC先停机、报警,因此,有必要将故障检测措施作为控制系统设计的一个必要的组成部分,以提高整个设备的可维修性。
一、故障检测
1.时限故障检测
由于设备在工作循环中,各工步运动在执行时都需要一定时间,且这些时间都有一定限度,所以可以用这些时间作为参考,在要检测的工步动作开始的同时,起动一个计时器,计时器的时间设定值比正常情况下该动作要持续的时间长20%-30%,而计时器的输出信号可以用于报警、显示或自动停机。当设备某工步动作的时间超过规定时间,达到对应的计时器预置时间,还未转入下一个工步动作时,计时器就会发出故障信号。该信号使正常工作循环程序停止,起动执行报警和显示程序。以三菱FX系列PLC为例,设某工序n的状态为M010,若此工序的运行时间为10秒,可以设置一个计时器T005,定时时间为12秒,用于监控工序n的情况,如图1所示。当工序n运行的时间超过12秒时,该程序会自动终止工序n的运行状态,并起动报警装置。
2.逻辑错误检测
在设备正常情况下,控制系统的各输入、输出信号、中间状态等之间存在着确定的逻辑关系。一旦设备出现故障,这种正常的逻辑关系便被破坏,而出现异常逻辑关系,必然是设备出现了故障。因此可以事先编制好一些常见故障的异常逻辑程序,加进用户程序中。一旦这种逻辑关系出现状态为“1”,就必然是发生了相应的设备故障,即可将异常逻辑关系的状态输出作为故障信号,用来实现报警、停机等控制。
例如,在正常情况下,机床动力头原位限位开关与向前进给运动的终点限位开关是不会同时被压下的,即两输入信号在正常情况下不可能为“1”状态,如果这两个输入信号的状态同时为“1”,则必然是至少有一个限位开关出现故障。因此,可以在程序中增加一条这两个信号相“与”并驱动某继电器的程序。当该继电器的状态为“1”时,PLC可在一个扫描周期时间里停机、报警。
二、故障显示
1.直接分别显示
无论上面哪种方式,具体的故障信号都是由专门的程序分别检测出来的。这些故障信号分别与某故障一一对应。这样,最简单的办法就是分别显示,即每个故障检测信号设置一个显示单元。这样做的好处是清楚,易于分辨故障点及故障元件;缺点是要增设很多的输出点,不但在经济上不合适,也可能因为PLC输出点不够又不能再增设而无法实现。
2.集中共用显示
所有的故障检测信号共用一个显示单元,或者是几个故障信号共用一个显示点。这种办法只显示有故障发生,而不能清楚地指示出故障的具体部位或元件,虽然可以节省PLC的输出点,但不能减轻判断、寻找故障点的工作量,不利于提高维修工作效率。
3.分类组合显示
这种做法是将所有的故障检测信号按层次分成组,每组各包括几种故障。例如,对于多工位的自动线的故障信号,可分为:故障区域(机号)、故障部件(动力头、滑台、夹具等)、故障元件等几个层次。当具体的故障发生时,检测信号同时分别送往区域、部件、元件等显示组,这样就可以指示故障发生在某区域、某部件、某元件上。
例如某自动生产线由三台单机组成,每台单机可分为左、右、立式动力头三个部件,每个部件分为原位、终点、进给超时及退回超时四种故障,共有36种故障组合。采用分类组合显示方法,可显示到具体的故障元件,使判断、查找方便。不仅可提高设备的维修效率,而且可节省输出显示点。具体的程序如图2所示,当线圈Y000、Y003和Y008都有输出时,就表示1号机左动力头进给超时故障。
总之,在PLC控制系统的设计中,选择合适的故障信号检测和故障信号显示方法,可以避免可能造成的设备事故,并大大提高整个设备的可维修性。
关键词: PLC 故障检测 故障显示
可编程控制器本身具有很高的可靠性,在CPU操作系统的监控程序中有完整的自诊断程序,万一出现故障,借助自诊断功能可以很快找到故障部位,确定故障所在。但PLC外部的输入输出元件就不那么可靠,如行程开关、电磁阀、接触器等的故障率就很突出,而当这些元件出现故障时PLC不会自动停机,直到故障造成后果,如机械顶死、控制系统常规保护动作之后才会有所反应。为了提高维修工作效率,特别是为了及时发现元件故障,在还没有酿成设备事故之前使PLC先停机、报警,因此,有必要将故障检测措施作为控制系统设计的一个必要的组成部分,以提高整个设备的可维修性。
一、故障检测
1.时限故障检测
由于设备在工作循环中,各工步运动在执行时都需要一定时间,且这些时间都有一定限度,所以可以用这些时间作为参考,在要检测的工步动作开始的同时,起动一个计时器,计时器的时间设定值比正常情况下该动作要持续的时间长20%-30%,而计时器的输出信号可以用于报警、显示或自动停机。当设备某工步动作的时间超过规定时间,达到对应的计时器预置时间,还未转入下一个工步动作时,计时器就会发出故障信号。该信号使正常工作循环程序停止,起动执行报警和显示程序。以三菱FX系列PLC为例,设某工序n的状态为M010,若此工序的运行时间为10秒,可以设置一个计时器T005,定时时间为12秒,用于监控工序n的情况,如图1所示。当工序n运行的时间超过12秒时,该程序会自动终止工序n的运行状态,并起动报警装置。
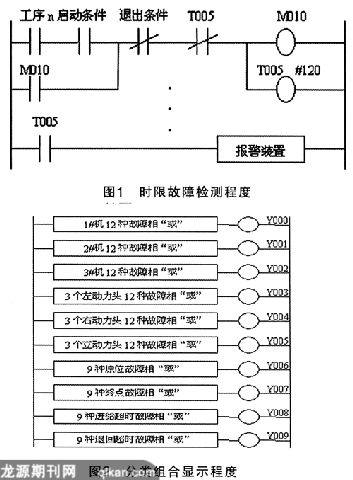
2.逻辑错误检测
在设备正常情况下,控制系统的各输入、输出信号、中间状态等之间存在着确定的逻辑关系。一旦设备出现故障,这种正常的逻辑关系便被破坏,而出现异常逻辑关系,必然是设备出现了故障。因此可以事先编制好一些常见故障的异常逻辑程序,加进用户程序中。一旦这种逻辑关系出现状态为“1”,就必然是发生了相应的设备故障,即可将异常逻辑关系的状态输出作为故障信号,用来实现报警、停机等控制。
例如,在正常情况下,机床动力头原位限位开关与向前进给运动的终点限位开关是不会同时被压下的,即两输入信号在正常情况下不可能为“1”状态,如果这两个输入信号的状态同时为“1”,则必然是至少有一个限位开关出现故障。因此,可以在程序中增加一条这两个信号相“与”并驱动某继电器的程序。当该继电器的状态为“1”时,PLC可在一个扫描周期时间里停机、报警。
二、故障显示
1.直接分别显示
无论上面哪种方式,具体的故障信号都是由专门的程序分别检测出来的。这些故障信号分别与某故障一一对应。这样,最简单的办法就是分别显示,即每个故障检测信号设置一个显示单元。这样做的好处是清楚,易于分辨故障点及故障元件;缺点是要增设很多的输出点,不但在经济上不合适,也可能因为PLC输出点不够又不能再增设而无法实现。
2.集中共用显示
所有的故障检测信号共用一个显示单元,或者是几个故障信号共用一个显示点。这种办法只显示有故障发生,而不能清楚地指示出故障的具体部位或元件,虽然可以节省PLC的输出点,但不能减轻判断、寻找故障点的工作量,不利于提高维修工作效率。
3.分类组合显示
这种做法是将所有的故障检测信号按层次分成组,每组各包括几种故障。例如,对于多工位的自动线的故障信号,可分为:故障区域(机号)、故障部件(动力头、滑台、夹具等)、故障元件等几个层次。当具体的故障发生时,检测信号同时分别送往区域、部件、元件等显示组,这样就可以指示故障发生在某区域、某部件、某元件上。
例如某自动生产线由三台单机组成,每台单机可分为左、右、立式动力头三个部件,每个部件分为原位、终点、进给超时及退回超时四种故障,共有36种故障组合。采用分类组合显示方法,可显示到具体的故障元件,使判断、查找方便。不仅可提高设备的维修效率,而且可节省输出显示点。具体的程序如图2所示,当线圈Y000、Y003和Y008都有输出时,就表示1号机左动力头进给超时故障。
总之,在PLC控制系统的设计中,选择合适的故障信号检测和故障信号显示方法,可以避免可能造成的设备事故,并大大提高整个设备的可维修性。